Equipment for wood waste, peat, hydrolytic lignin and other materials drying
Aerodynamical dryer – dispergator
We produce highly effective, compact and unique equipment for drying and desintegration of wood waste, peat and hydrolytic lignin in order to produce fuel granules, briquettes, fertile soil, and waste paper disintegration for ecovata (heat-insulating building material) production.
In a compact apparatus uninterrupted process of desintegration and drying of wood chips, shaving, and sawdust take place simultaneously up to necessary fractional structure and dryness. The principle of the apparatus work is based on the percussive influence of rotor on wood waste by intensive mass and air exchange that provides drying of the material.
The product is patented.
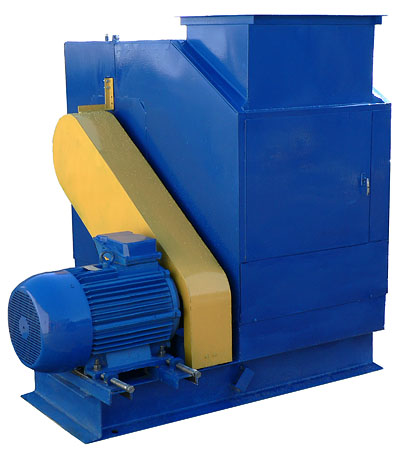
The aerodynamic dryer – dispergator simultaneously carry out drying and desintegration of wood waste and peat in order to get the mass for granulating into pellets (fuel granules) and for briquetting. As well as this it is possible to dry and crumble up rind in order to burn it, dry desintegration of waste paper in order to get heat insulation and other materials, sawmilling and drying of accumulation of pulp and paper enterprises for producing building materials, desintegration of wood waste in order to get wood flour and polyethylene terephthalate bottles grinding for getting polyethylene terephthalate flakes.
Dispersion and drying of wood waste is carried out in aerodynamical dryer – dispergator (crushing machine). The turning rotor with radial blades produces vortex motion of the air in the apparatus. The product separation occurs in the following way. Fine and dry fragments are taken away from the apparatus while coarse and wet fragments stay in it up to the end of the drying and desintegration processes.
The process of grinding is determined by structural and technical settings of the dispergator.
Drying of the material is provided by the intensive mass and air exchange that is the result of the apparatus engineering solution, in addition to it the process of drying is expedited in connection with intensive friction of the particles in the thick layer when they move in the dispergator with a high circular velocity.
The product was awarded by the silver medal at the international contest of inventions in Paris in 2003 and the bronze medal at the world exhibition of innovations, inventions and new technologies in Brussels in 2002.
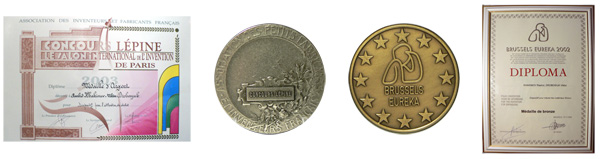
Producing modifications of the equipment:
- The equipment for wood waste processing in order to get mass for pellets (fuel granules) and briquettes granulating.
- The equipment for peat processing in order to produce pellets, briquettes and rich soil.
- The equipment for producing ecovata out of newsprint and other kinds of paper waste.
The equipments arrangement:
- Aerodynamical dryer – dispergator
- High pressure ventilator (special version)
- Cyclones (original)
- Air ducts (according to the customer’s technical request)
- Power box with the frequency converter (Schneider Electric company)
- Control console
Theoretical preconditions
The drying of wet materials is a very expensive and difficult process.
The main aim of drying of wood waste (sawdust, shaving, wood chips and rind), peat and other materials those may be used as energy resources is to increase their thermal value.
In the process of drying the removal of moisture out of materials is carried out by means of exhalation and withdrawal of generated steams.
All dryers are classified, generally, by the ways of warmth admission to the surface of the drying materials. There are contact, convection, radiation, sublimation, high-frequency and combined dryers.
Convection dryers are more effective for dispersed materials as desiccative agent has a continuous contact with wood waste and peat surface.
Depending on the materials characteristics and the size of fragments there are different constructions of the dryers: drumming, belt, with a “boiling” layer, aero fountain and others.
Heated air or smoke gases are used as desiccative agent. As it is impossible to get “clear” product when smoke gases are used, the drying equipment must have heat exchanger, where atmospheric air will be heated.
The speed of drying process depends on the temperature of desiccative agent, relevant speed of its moving, specific surface of the drying fragments and physical characteristics of the material.
At the beginning of the drying process (a constant speed of drying period) the humidity of the material is constant at large. After a certain period of time when the concentration of moisture at the material surface goes down as the result of exhalation, the period of falling drying speed and the temperature of the material begins to increase. As moisture content goes down the temperature of the dryable fragments approximates to the temperature of desiccative agent.
Thus there are some limits for the temperature of the used desiccative agent in connection with the possibility of fine- dyspersated dry wood and peat fragments ignition.
Fine-dyspersated wood waste (sawdust) contains some amount of coarse inclusions (wood chips). As the result of drying when the technical settings are adjusted to moisture removal out of sawdust wood chips will have heightened moisture content. Preliminary grinding of the wet raw material in order to smooth the fractionating structure is hampered in connection with structural peculiarities of mills. The mostly widespread mills are hammer, where the separation of the ready-made product is carried out through the sieve. The humid wood fragments stick to it and the taking away of the product is stopped.
The speed of the desiccative agent in hammer, belt, with “boiling” layer and aero fountain dryers is limited by the speed of the particles soaring and forms 0.5 – 2.0 meters per second. In case the speed of the agent is increased the fragments will be taken away in a humid condition.
As it was necessary to increase the effectiveness of wood waste and peat drying a compact aerodynamical dryer – dispergator has been created. In this kind of dryer efficient process of drying and desintegration of coarse wood particles occurs simultaneously.
Drying of the material is provided by the intensive mass and air exchange that is the result of the apparatus engineering solution, in addition to it the process of drying is expedited in connection with intensive friction of the particles in the thick layer when they move in the dispergator with a high circular velocity. In drum dryers the temperature of the desiccative agent is about 400°C that may cause the ignition of the raw material. The drum is inert and its starting needs a considerable time and it is difficult to regulate the process of drying.
Aerodynamical dryer works by the 120-150°C temperature of the agent that prevents the wood and peat fragments from ignition. The dryer starts in a few minutes and the process of burning is easily regulated.
The process of desintegration is carried out by intensified influence of revolving rotor up to the necessary granulometric structure; the process of drying of wood waste goes on at the same time. The ready-made grinded and dried product is taken away from the center of the apparatus by the influence of the inertial power. The size of the ready-made particles is easily regulated. Aerodynamical separation gives an opportunity to get the product of necessary uniform moisture.
Desiccative agent speed concerning the material fragments in the aerodynamical dryer is 25-28 meters per second that allows to dry wood waste and peat in a compact apparatus taking not much of production area and having a low metal content construction.